Well it’s no question that Cerakote has been the industry standard for coating firearms. But as of the last two years more and more firearms are being coated with a coating called PVD (Physical Vapor Deposition). It started a while back when a company called Cryptic Coatings came out with these super slick bolt carrier groups for the AR15 and AR10 platforms. These bolts were coated in the process called PVD, and in my personaly opinion I have been extremely impressed with durability and how well the coating holds up…especially as being on a BCG. I have had two bolts with these coatings on them and one bolt with Cerakote on it. Over the last 5 years I have only seen wear on the Cerakote bolt and carbon sticks to the Cerakote bolt. Now my Cryptic Coatings PVD/CVD BCG’s have had no wear on them and the carbon wipes right off with the swipe of my finger. Below is my 300 Blackout Cerakoted in black with a Cryptic Coatings Mystic Silver BCG.
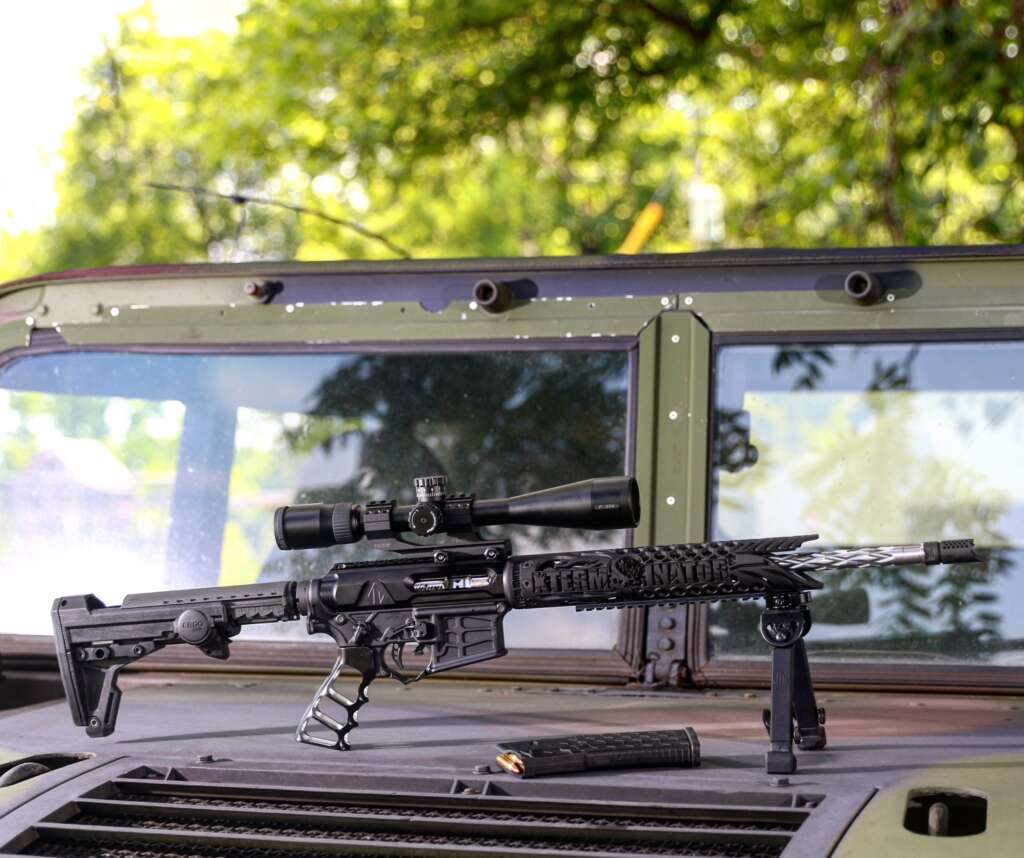
Cerakote
Manufactures and customers alike demand the most out of their finish. Exposure to corrosive environments, wear and abrasion, as well as chemical abuse, takes its toll on parts and finished goods. Cerakote ceramic coatings are a premium upgrade and an excellent alternative to PVD (Physical Vapor Deposition), Ionbond, and DLC coating (diamond-like carbon coating).
Cerakote is the industry innovator in ceramic coating technology offering unmatched corrosion protection, and chemical and abrasion resistance, all in an ultra-thin film ceramic-based coating. Cerakote can be applied to most surfaces and offers hundreds of different color options. Cerakote is easily applied both manually and automated, in a simple, single coat process (no base coat or top coat required).
PVD/CVD
PVD is the abbreviation of Physical Vapor Deposition. PVD is a process that produces a family of coatings. The staple of the family is titanium nitride (TiN) however: chromium nitride (CrN), aluminum titanium nitride (AlTiN) are other examples of PVD coatings. This technology gained popularity in the 70’s when the military adapted it to solve a wide range of issues regarding friction and wear of metal parts. The term physical vapor deposition was first used in 1966 but the process can be traced back as far as 1838 to a scientist named Michael Faraday. The most current version of physical vapor deposition was completed in 2010 by NASA scientists at the NASA Glenn Research Center in Cleveland, Ohio. The process is carried out in high vacuum chambers, well below atmospheric pressures.
CVD is the abbreviation Chemical Vapor Deposition. Chemical vapor deposition is a chemical process used to produce high-purity, high-performance solid materials. One such material is Diamond-Like-Carbon (DLC). Since 1952 when William Eversole grew the first diamond in a vacuum chamber, DLC thin film use has grown tremendously. DLC coatings feature excellent hardness, wear and low friction properties under dry or deficient lubrication conditions. They are ideally suited for mechanical assemblies with sliding and rolling movements
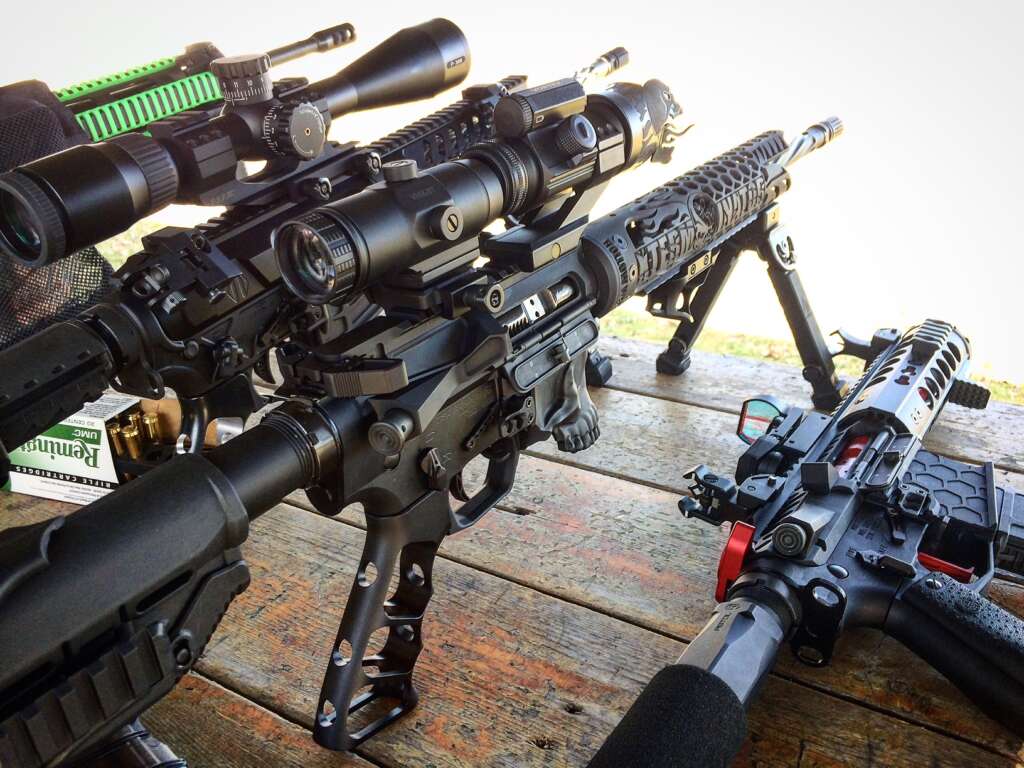
It’s really hard to say one coating is better than the other.
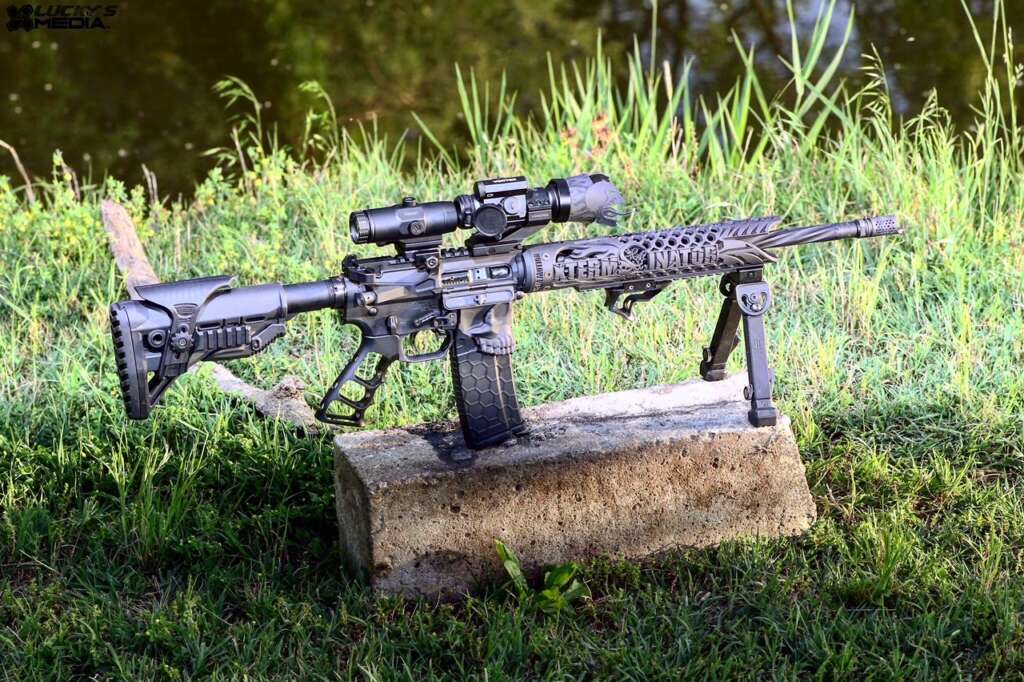
So, In conclusion. If I had to chose, I would stick to Cerakote for all my exterior coatings and for my Bolt Carrier Group and charging handle….I would choose PVD/CVD. Simply because these parts perform better when they are slicker and they tend to get the most carbon build up. Cleaning the PVD/CVD part is also easier since you don’t need to scrub at all. It’s a great feeling having PVD/CVD parts in your firearm knowing they wont wear or tear no matter how extereme you get….I mean with a hardness of 3000 Vickers and being able to withstand up to 1,100° F…its difficult to not have your internal moving parts coated in PVD/CVD.